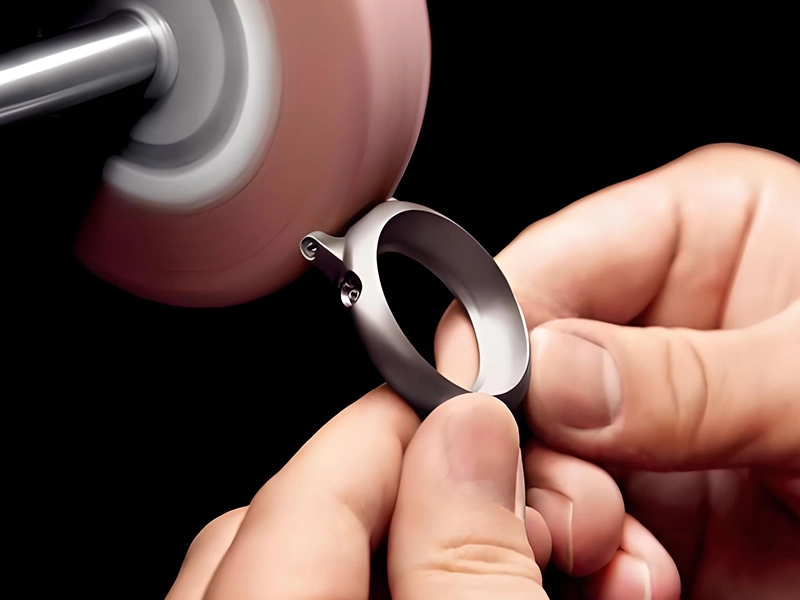
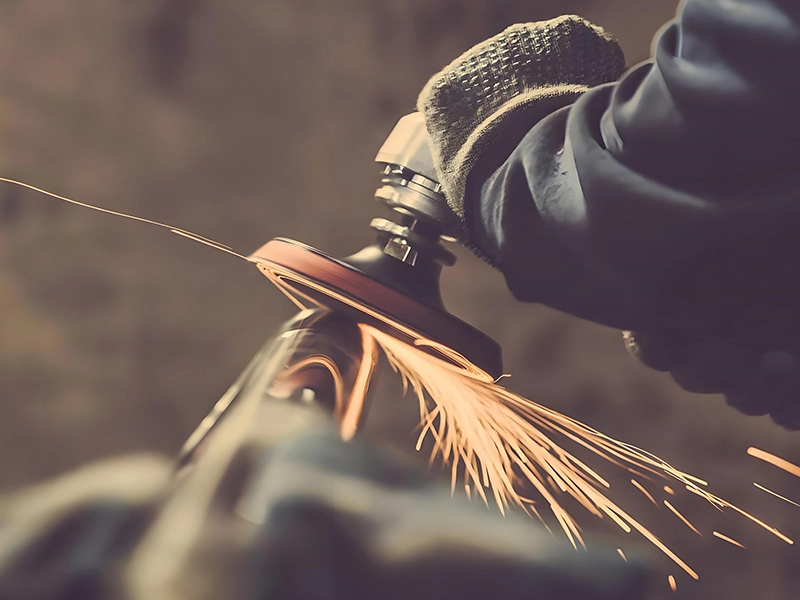
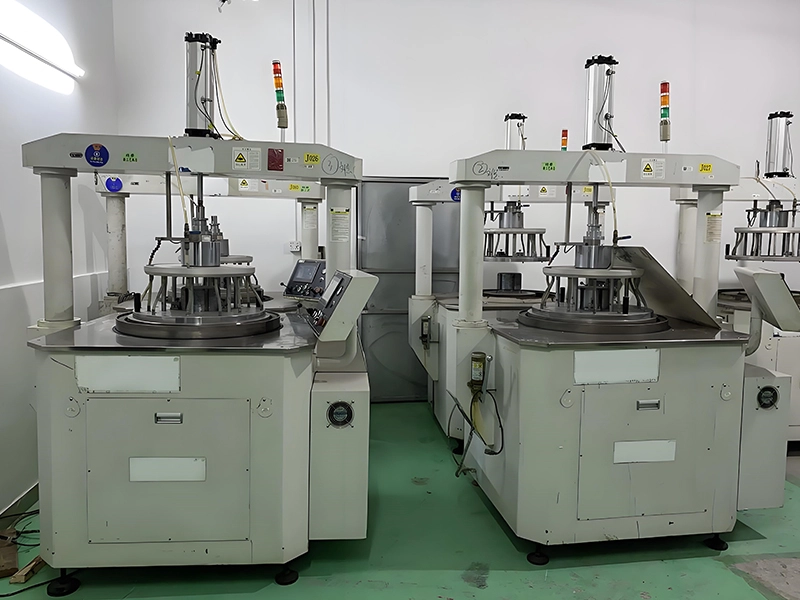
Surface Polishing
Surface polishing is one of the very important processes for surface treatment of many products, and the quality of polishing directly affects the final surface treatment effect of the product. For example, PVD, anodizing, electroplating, etc. all require polishing. At Precious, we have experienced manual polishing workers and automated polishing equipment, with extensive experience in polishing various materials including aluminum alloys, stainless steel, and titanium alloys.
What Is Surface Polishing?
Polishing refers to the processing method of using mechanical, chemical, or electrochemical actions to reduce the surface roughness of a workpiece, in order to obtain a bright and smooth surface. It is a modification process of the surface of a workpiece using polishing tools and abrasive particles or other polishing media.
Polishing cannot improve the dimensional or geometric accuracy of the workpiece, but aims to obtain a smooth surface or mirror gloss.
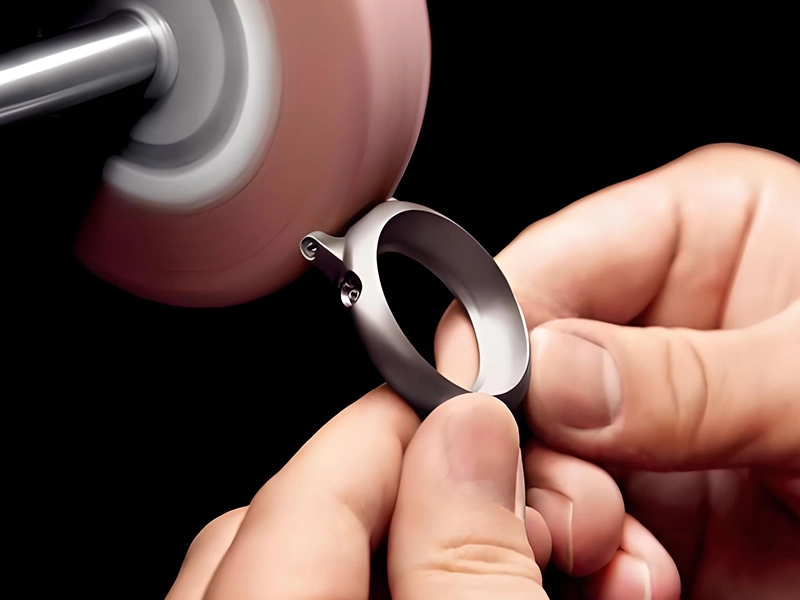
What Types of Surface Polishing Are There ?
Mechanical polishing is a polishing method that obtains a smooth surface by cutting and plastic deformation of the material surface to remove the convex parts after polishing. Generally, oilstone strips, wool wheels, sandpaper, etc. are used, and manual operation is the main method
Polishing is achieved by rolling and micro cutting the surface of the workpiece using a high-speed rotating flexible polishing wheel and extremely fine abrasives. The polishing wheel is made of multiple layers of canvas, felt, or leather and is used for polishing larger parts.
Chemical polishing is the process of allowing the micro protruding and concave parts of a material to dissolve preferentially in a chemical medium, resulting in a smooth surface. The main advantage of this method is that it does not require complex equipment, can polish workpieces with complex shapes, can polish many workpieces at the same time, and has high efficiency. The core issue of chemical polishing is the preparation of polishing solution. The surface roughness obtained by chemical polishing is generally around 10 μ m
What Are The Commonly Used Polishing Materials?
Sandpaper: Sandpaper is a material used for manual grinding and polishing, typically composed of adhesive paper and abrasive. Coarse sandpaper is suitable for removing large surface defects, while fine sandpaper is used to polish the surface and make it smooth. Sandpaper is suitable for surface treatment of softer metal and non-metal materials.
Grinding wheel: A grinding wheel is a material used for mechanical polishing, which can be used to remove pits and defects on the surface of materials. Grinding wheels are usually composed of abrasives and binders, with abrasives such as quartz sand, alumina, silicon carbide, etc. Grinding wheels are suitable for surface treatment of harder metals such as stainless steel, cast iron, etc.
Polishing cloth is a material used for manual and mechanical polishing, typically a textile containing abrasives. Polishing cloth is suitable for polishing and removing scratches on surfaces of different materials.
Aluminum oxide and silicon dioxide
Aluminum oxide and silicon dioxide are abrasive materials suitable for efficient grinding and polishing of metal surfaces. Silicon dioxide is finer than aluminum oxide and can better remove small surface defects. These two types of abrasives are generally used for mechanical liquid polishing.
Advantages of Surface Polishing
- Improve the appearance of the product surface treatment to ensure that there are no defects on the surface after anodizing or PVD, meeting the appearance standards of consumers.
- Polishing some injection molds can make the products produced by the molds smooth and improve the appearance quality of the products.
- Increase wear resistance:For surfaces that are prone to wear, such as bearings, gears, and cutting tools, polishing can improve their hardness and wear resistance.
- Improve optical performance:For products that require high-precision optical performance, such as lenses, mirrors, and optical instruments, polishing can improve their surface smoothness, thereby reducing phenomena such as reflection, refraction, and dispersion.
- 510, Building M, Flying Pigeon Industrial Park, No. 1223 Guanguang Road, Guanlan Street, Longhua District, Shenzhen, Guangdong, China
- +8618688772802
- info@precionn.com