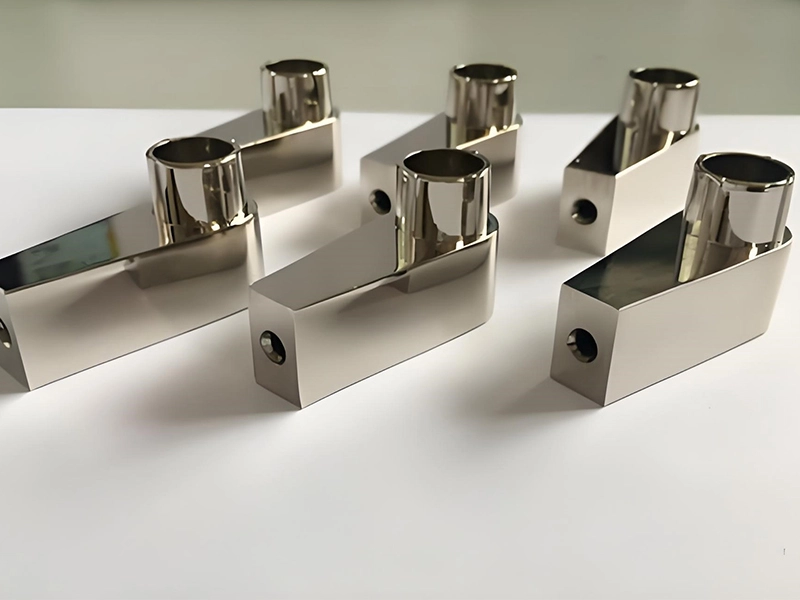
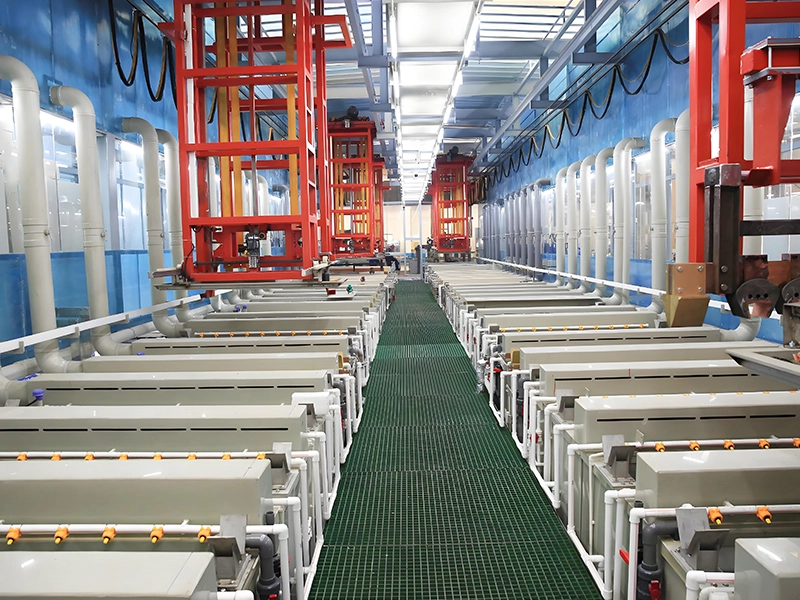
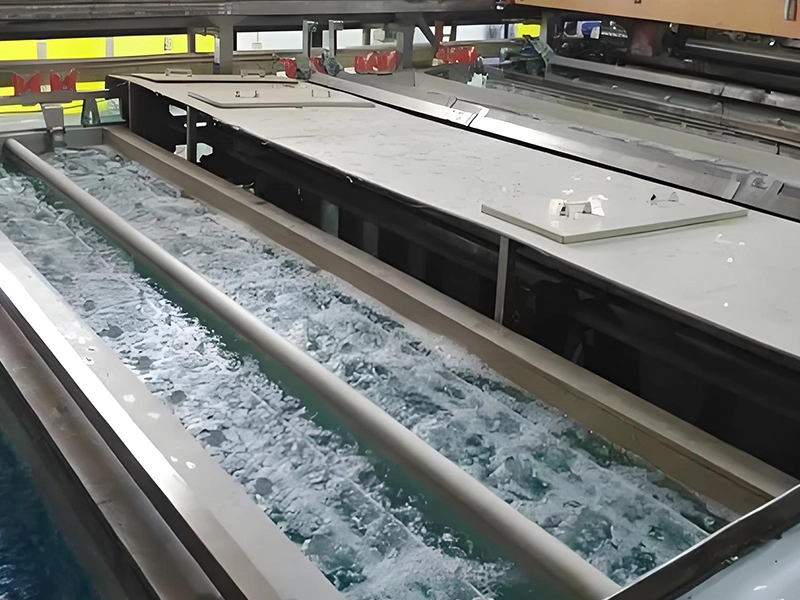
Surface Plating
Precionn’s electroplating workshop is located in a professional environmental protection industrial park with specialized sewage treatment facilities. Capable of electroplating more than 10 types of metal surface coatings, improving product surface hardness, preventing wear, enhancing conductivity, smoothness, heat resistance, and surface aesthetics.
What is Electroplating?
Electroplating is the process of using the principle of electrolysis to deposit a thin layer of other metals or alloys on certain metal surfaces. It is a process of using electrolysis to attach a layer of metal film to the surface of metal or other material parts, thereby preventing metal oxidation (such as rust), improving wear resistance, conductivity, reflectivity, corrosion resistance (such as copper sulfate), and enhancing aesthetics.
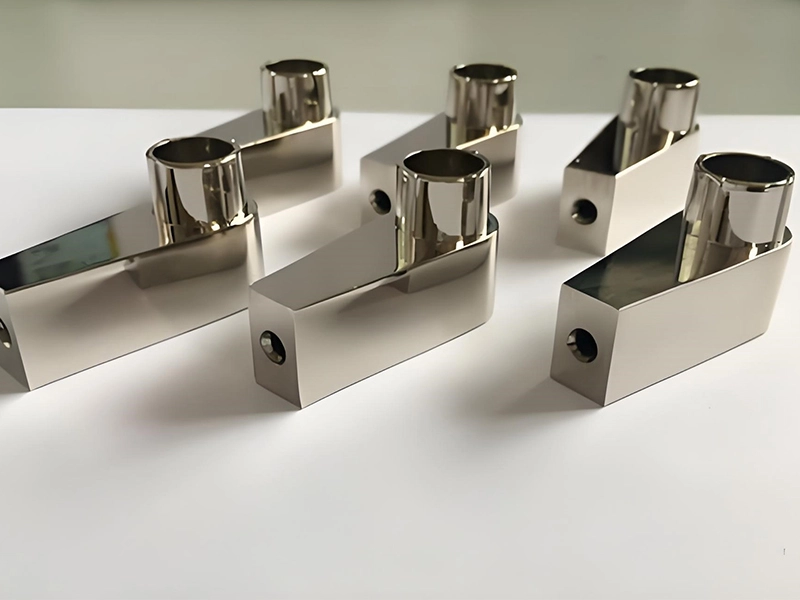
Applications of Surface Plating
Galvanization is mainly used in screws, circuit breakers, and industrial products.
Nickel plating is mainly used for energy-saving lamp heads, aluminum alloy or alloy steel parts of industrial automation equipment.
Chromium plating is applied to bright decorative parts of bathroom appliances and steel parts of mechanical equipment.
Gold plating is applied to key components such as jewelry decorations, connectors, circuit boards, etc.
Silver plating is applied to key components such as jewelry decorations, connectors, circuit boards, etc.
What Are The Types of Plating Processes?
Galvanization: The main method used is hot-dip galvanizing, which has a low cost, average corrosion resistance, and a silver white color.
Nickel plating: Nickel plating can be used as a protective decorative coating on the surfaces of steel, aluminum alloys, and zinc die-casting parts to protect the substrate material from corrosion or to provide a bright decorative effect. The color is silver white or bright yellow.
Chrome plating: Chrome plating has high hardness and good wear resistance, but its rust prevention ability is not as good as nickel plating and zinc plating.
Gold plating: improves conductive contact impedance and enhances signal transmission.
Silver plating: improves conductive contact impedance and enhances signal transmission.
Advantages of Surface Plating
- Good surface quality of electroplating: Electroplating can form a dense metal layer on the surface of the original substrate, with good surface smoothness and uniformity. Due to the good adhesion of the electroplating layer, it is not easy to peel off or age, effectively extending the service life of the metal.
- Excellent corrosion resistance: and wear resistance After coating the surface of a metal with another metal, a new chemical element can be formed, effectively improving the corrosion resistance and wear resistance of the metal. For example, parts plated with nickel can better resist corrosion, while parts plated with chromium can be more wear-resistant.
- Low manufacturing:cost Compared to other quality surface treatment techniques, electroplating has the advantages of low cost, easy operation, and high production efficiency. In addition, electroplating also has the ability to handle large-sized and complex workpieces.
- 510, Building M, Flying Pigeon Industrial Park, No. 1223 Guanguang Road, Guanlan Street, Longhua District, Shenzhen, Guangdong, China
- +8618688772802
- info@precionn.com