Powder Metallurgy
Do you want to use a low-cost manufacturing process for small metal parts with complex shapes and large quantities? You can choose Precionn. We have a professional powder metallurgy technical team and equipment that can provide the entire product process from evaluation, metal injection mold design, mold manufacturing, metal injection molding, degreasing, sintering, shaping to finished products. The products we manufacture cover the mechanical tool industry, medical industry, consumer electronics industry, and auto parts industry.
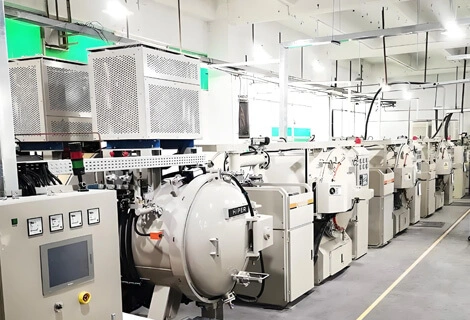
Application of Powder Metallurgy
1. Application of traditional powder pressing forming: Powder pressing technology has a high material utilization rate and reduces the secondary processing of subsequent products. It mainly produces some parts with complex shapes such as gears, shafts, blades, etc.
2. Application of metal injection molding:
Consumer electronics field. SIM card trays, camera brackets, power interfaces, etc. for smartphones and tablet computers, hinge components for folding mobile phones, casings for smart wearable products, and other parts.
Auto parts. Turbocharger parts, adjustment rings, injector parts, blades, gearboxes, power steering parts, etc.
Medical equipment. Surgical handles, scissors, forceps, dental parts, orthopedic joint parts, etc.
Power tools: The processing of power tool parts is very complex, the processing cost is high, the material utilization rate is low, and the dependence on MIM is high. Typical products include special-shaped milling cutters, cutting tools, fasteners, and micro gears developed in recent years. , Loose cotton machine/textile machine/curling machine parts, etc.
Advantages of Powder Metallurgy
1. Unlimited structure: complex metal parts can be directly formed like plastic injection molding, allowing free design of three-dimensional shapes. In theory, all shapes that can be molded by plastic can be realized through the MIM process;
2. Reliable physical properties: the product has uniform structure and good density, the density can reach more than 98% of the theoretical density, and the product has high mechanical properties such as strength, hardness, and elongation;
3. High product precision: the dimensional accuracy of the product once formed can reach +/-0.2mm, and products with general precision requirements do not require post-processing;
4. The batch cost advantage is significant: Compared with other processes, especially for products with complex structures, the near-net shape process has a significant cost advantage in mass production using the MIM process.
- 510, Building M, Flying Pigeon Industrial Park, No. 1223 Guanguang Road, Guanlan Street, Longhua District, Shenzhen, Guangdong, China
- +8618688772802
- info@precionn.com