Mold Design and Manufacturing
Precionn is an excellent mold manufacturer in China. The company has precision manufacturing equipment, including five-axis machining centers, wire cutting, electrical discharge machining equipment, surface grinding equipment, optical grinding equipment, etc. Mold materials can meet different customer needs. The material supplier is China’s largest steel producer. The company has a professional mold design team and assembly and debugging team. It is guaranteed that the mold delivered to you can be produced normally. Our company can not only provide cost-saving prototype molds, but also mass-produced mass production molds. The main mold types include: injection molds, hot stamping molds, die-casting molds, etc.
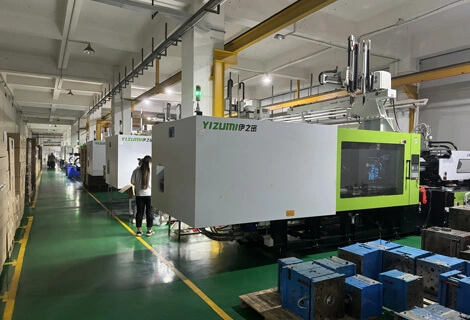
Injection molds include metal injection molds and plastic injection molds. Injection molds are mainly used in injection molding processes. They have short production cycles and high production efficiency. They can produce some products with complex shapes and high dimensional accuracy, especially some products with inserts, and can achieve Automated production.
Stamping molds are a key factor in ensuring the shape and size of stamping process products. Stamping can be produced with high efficiency and can achieve automated production. Stamping molds have a very high cost advantage for the mass production of thin parts. For multi-shaped products, continuous mold production can be used to ensure product accuracy and high-efficiency production.
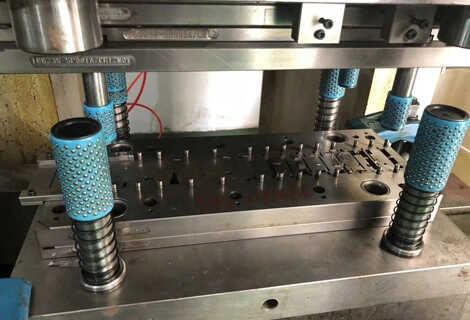
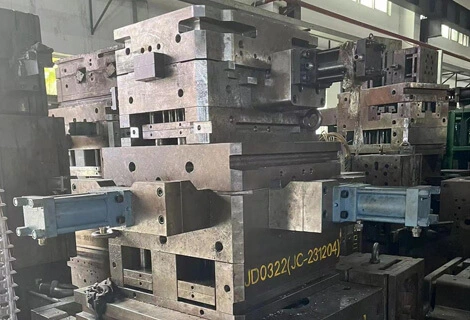
For some products with relatively large demand, we will help customers develop cost-saving processes. If it is aluminum, zinc alloy, magnesium alloy, we will use the die-casting process. Precionn can manufacture high-precision, long-life die-casting molds.
Advanced Technologies of Mold Design and Manufacturing
Mold processing mainly includes the following advanced processing methods:
1. CNC milling. Five-axis high-speed milling makes the processing of complex three-dimensional parts almost a reality, and the hardness of the material is no longer a limiting issue. The main cavity and surface of the plastic mold are completed by cnc milling. High-speed milling can process 60HRC hardened mold steel parts. Therefore, high-speed milling allows cutting after heat treatment, greatly simplifying the mold manufacturing process.
2. Slow wire cutting processing. Slow wire cutting is mainly used for processing two-dimensional and three-dimensional ruled surface parts such as various punch dies, injection molds, and die-casting moulds. In mold processing, slow wire cutting is an indispensable key technology. The processing of many precision holes such as punches, punch fixing plates, concave molds and discharge plates of stamping molds. In injection mold manufacturing, common applications include inlays. Processing of part holes, ejector holes, inclined ejector holes, cavity corners and slide blocks, etc.
3. Electrical discharge machining. EDM is suitable for processing complex parts such as precision small cavities, narrow slits, grooves, and corners.
4. Grinding machine processing. The grinding machines used in mold processing are mainly surface grinders, universal internal and external cylindrical grinders, and coordinate grinders (PG optical curve grinders). The optical curve grinder can grind workpieces such as connector die blades and punches, terminals, precision half-stroke punches, lower die inserts and stripper plate inserts.
5. Rapid clamping and positioning system and automation. It achieves unified reference exchange for milling, turning, measuring, EDM and other processes. It only takes about one minute to quickly complete the clamping and alignment of the electrode on the machine tool. The repeatable positioning accuracy is within 3 μm, minimizing the time required for installation. The fixed time greatly improves the actual running time of the machine tool.
Considerations When Carry Out Mold Design and Manufacturing
1. Provide comprehensive DFM report evaluation based on customer products and develop reasonable processes.
2. Mold material and hardness: Choose a mold base material that meets the standards. The molded parts material should be corrosion-resistant or anti-corrosion measures should be taken. The hardness should not be less than 50HRC or the surface hardening hardness should be higher than 600HV.
3. Mold structural design: Consider the shape of the mold cavity, cooling system, exhaust system and other factors to ensure that there are no defects when the product is formed.
4. Surface treatment of the mold: The fine surface treatment of the mold is crucial to the appearance quality of the product. Use appropriate surface treatment technologies, such as polishing, electroplating, etc., to ensure that the product surface is smooth and flawless.
- 510, Building M, Flying Pigeon Industrial Park, No. 1223 Guanguang Road, Guanlan Street, Longhua District, Shenzhen, Guangdong, China
- +8618688772802
- info@precionn.com