Metal Injection Molding
Metal powder injection molding technology is an advanced manufacturing technology in powder metallurgy. Precious has been deeply involved in powder metallurgy for many years and has rich experience in powder metallurgy manufacturing. For the new MIM manufacturing technology, we can quickly provide DFM evaluation reports and timely quotations, specializing in the manufacturing of metal small parts with irregular structures and high precision requirements.
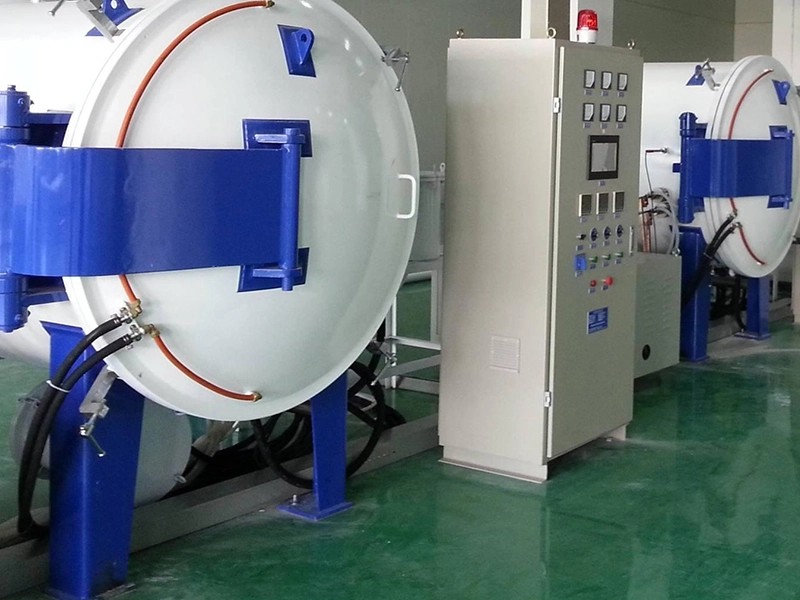
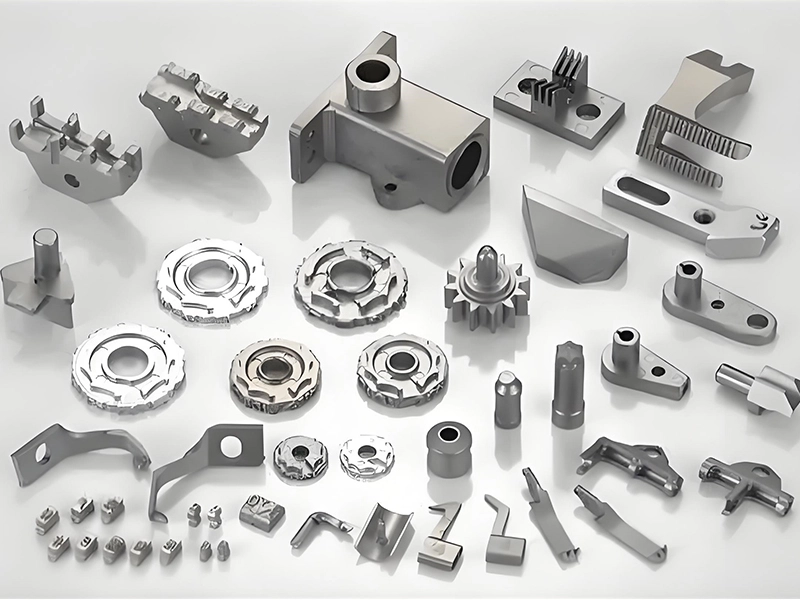
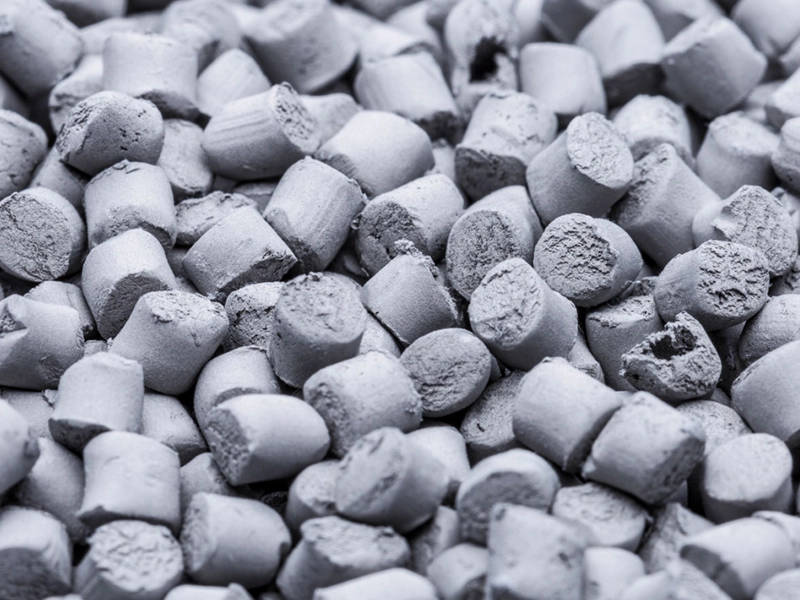
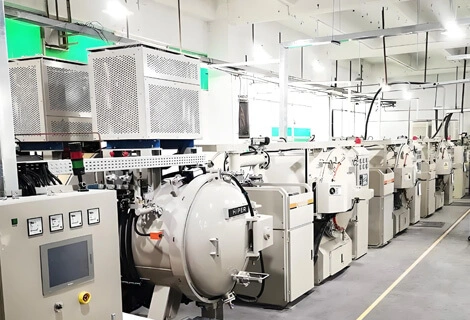
What is Metal Powder Injection Molding (MIM) ?
Metal Powder Injection Molding Technology (MIM) is a new type of powder metallurgy near net forming technology that introduces modern plastic injection molding technology into the field of powder metallurgy.
Firstly, the solid powder is uniformly mixed with organic binder, and after granulation, it is injected into the mold cavity through an injection molding machine in a heated and plasticized state (150 ℃) to solidify and form. Then, the binder in the formed billet is removed by chemical or thermal decomposition, and finally, the final product is obtained by sintering densification. Compared with traditional craftsmanship, it has the characteristics of high precision, uniform organization, excellent performance, and low production cost
Material Selection of Metal Powder Injection Molding (MIM)
316L stainless steel, 17-4PH stainless steel, 304 stainless steel, 440C stainless steel.
Iron based (commonly used materials Fe-2Ni, Fe-8Ni)
TC4 alloy
Applications of Metal Powder Injection Molding (MIM)
Consumer electronics industry: built-in connectors for mobile phones, SIM card holders, camera rings, hinge components for foldable phones, watch cases for smart wearable devices, watch buckles, etc.
Medical device industry: surgical handles, scissors, tweezers, dental parts.
Automotive industry: ignition switch for engines, ignition connection rails, fuel injectors.
Tools: such as drill bits, cutting heads, nozzles, gun drills, spiral milling cutters, punches, sockets, wrenches, electrical tools, hand tools, etc
Advantages of Metal Powder Injection Molding (MIM)
- Producing small metal parts with complex shapes like plastic products, suitable for manufacturing small parts with complex geometric shapes, high precision, and special requirements, usually weighing between 0.2-200g.
- It can directly form thin-walled structural components, and the shape of the product is close to or meets the requirements of the final product. The dimensional tolerance can generally be maintained at a level of ± 0.05mm.
- Compared with traditional mechanical processing and precision casting, the internal structure of the product is more uniform; Compared with traditional powder metallurgy pressing and sintering, the product has superior performance, high dimensional accuracy, and good surface smoothness (surface roughness can reach Ra0.80-1.6 μ m), without the need for further processing or only requiring a small amount of precision processing.
- The material has a wide range of applications, including ferroalloys, superalloys, titanium alloys, copper alloys, refractory metals, hard alloys, ceramics, and metal based composite materials. The product density is high (up to 95% to 99%), and the composition is
- 510, Building M, Flying Pigeon Industrial Park, No. 1223 Guanguang Road, Guanlan Street, Longhua District, Shenzhen, Guangdong, China
- +8618688772802
- info@precionn.com