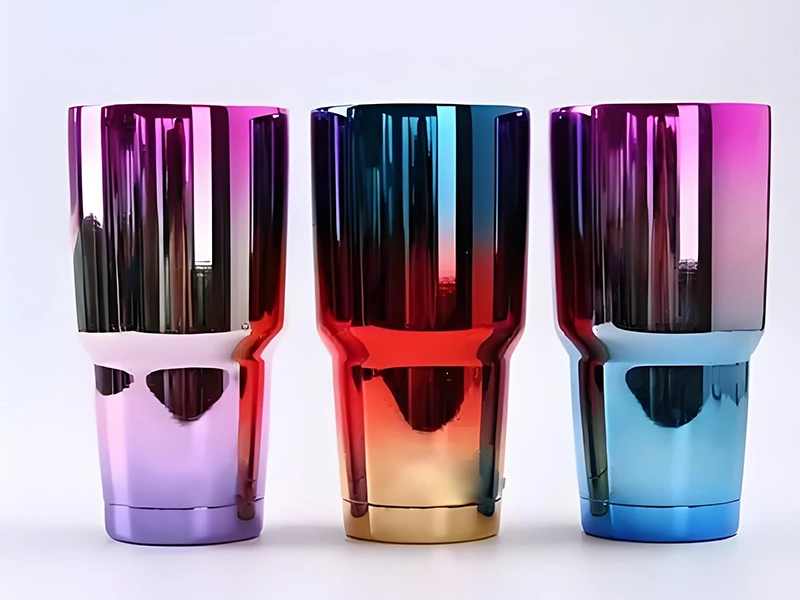
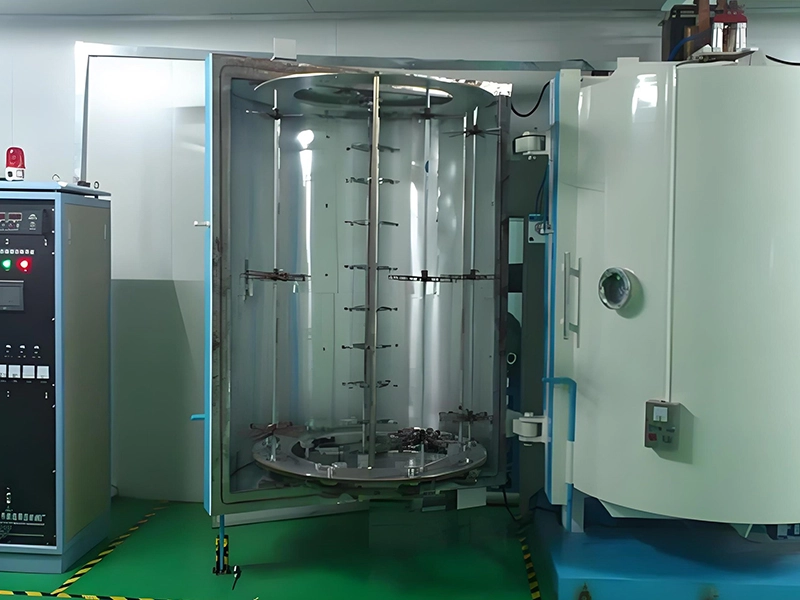
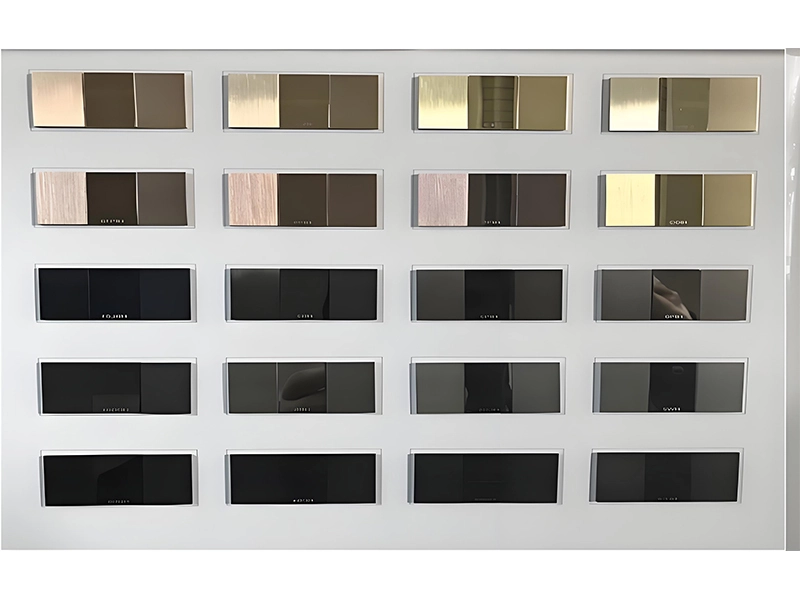
Custom PVD Coating
What is PVD Coating ?
PVD stands for Physical Vapor Deposition, which is a technology that vaporizes and deposits materials on the surface of a substrate under vacuum conditions through a physical process to form a thin film. This method can be performed at lower temperatures with minimal thermal impact on the substrate material, making it suitable for surface treatment of various materials.
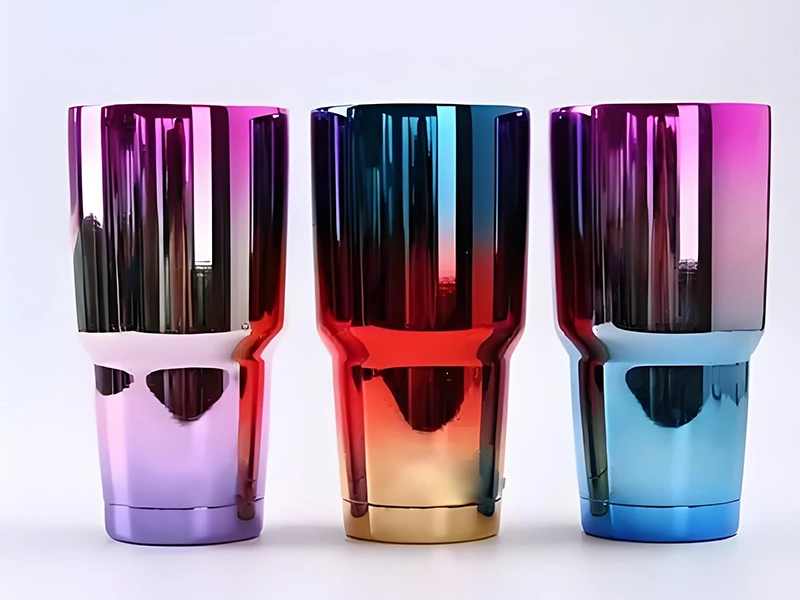
Which Materials Are Suitable For PVD Coating?
Aluminum alloy, stainless steel, alloy steel can all be PVD coated.
Common engineering plastics such as ABS, PC, PP, PMMA, PA, PS, PET, etc. can be coated with metal films on their surfaces using PVD processing.
Application of Custom PVD Coating
Decorative coating
PVD technology is widely used in the field of decorative coatings, including but not limited to phone cases, watches, jewelry, and glasses. Through PVD technology, various colored metal films such as gold, silver, blue, etc. can be deposited on the surface of these items, which are not only beautiful but also wear-resistant, greatly improving the added value and market competitiveness of the products.
Tool and mold coating
PVD technology is widely used in the tool and mold manufacturing industry. By depositing hard films such as titanium nitride (TiN), titanium carbide (TiC), etc. on the surfaces of cutting tools, drills, molds, etc., the hardness, wear resistance, and corrosion resistance of tools are significantly improved, and the service life of tools is extended.
Semiconductor industry
PVD technology is used in the semiconductor manufacturing process to deposit thin films of metals and insulating layers, such as aluminum, copper conductive lines, and silicon oxide insulating layers. These films play a crucial role in the manufacturing of integrated circuits, affecting the performance and reliability of chips.
Advantages of Custom PVD Coating
- Environmentally friendly and pollution-free: Compared to traditional chemical deposition methods such as electroplating, PVD technology produces almost no harmful substances, greatly reducing environmental pollution.
- High hardness and wear resistance: PVD coatings have high hardness and good wear resistance, suitable for various high-strength working environments.
- High quality surface film: The PVD process is carried out in a high vacuum environment, which can effectively control the composition and structure of the film, producing high-quality films with high purity, good crystallinity, and strong adhesion.
- 510, Building M, Flying Pigeon Industrial Park, No. 1223 Guanguang Road, Guanlan Street, Longhua District, Shenzhen, Guangdong, China
- +8618688772802
- info@precionn.com