CNC Milling and Turning
Turning and milling is an advanced cutting method using the combined motion of milling cutter rotation and workpiece rotation to achieve the cutting of the workpiece, so that the workpiece can meet the requirements of shape accuracy, position accuracy and the integrity of the machined surface. Composite processing shortens the product manufacturing process chain and improves production efficiency. Can install a variety of special tools, new tool arrangement, reduce tool change time, improve processing efficiency, reduce the number of clamping, improve product accuracy.
Timely quotes and free DFM evaluation
Tolerance level can be 0.005mm
The diameter of the machined parts is D1mm~D25mm
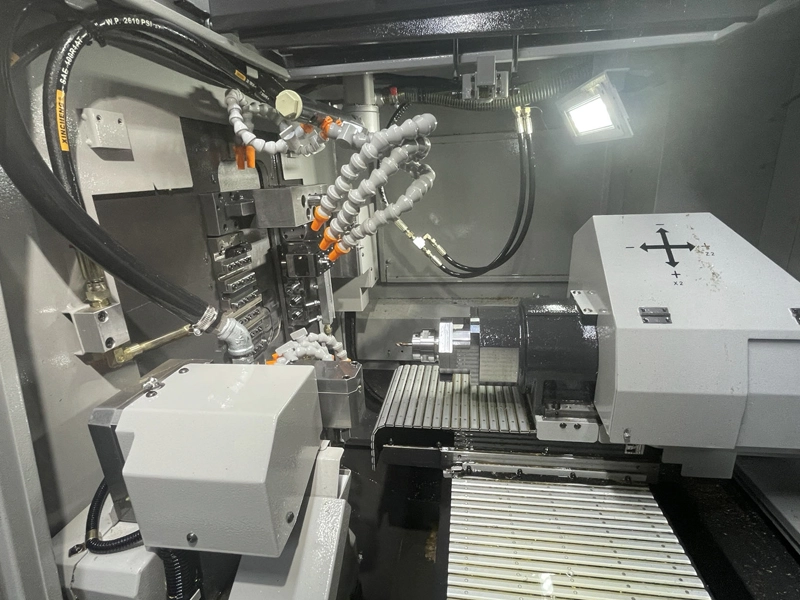

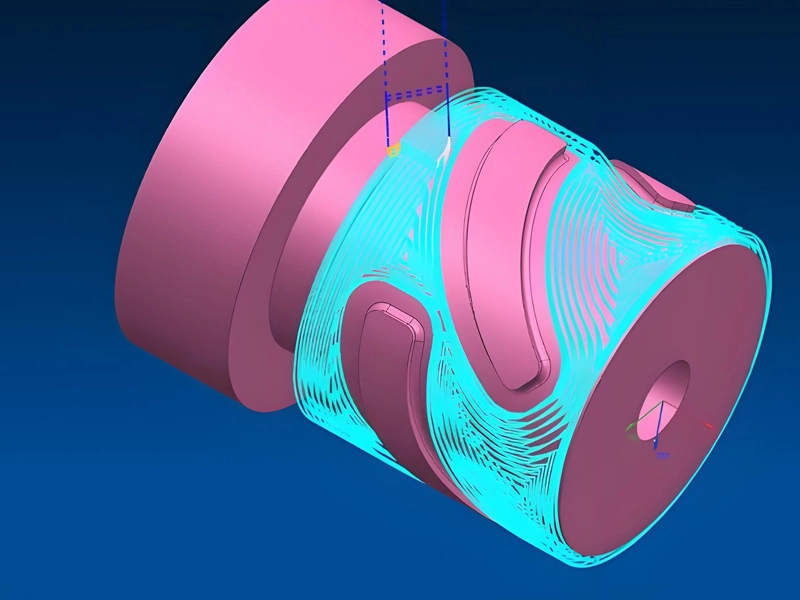
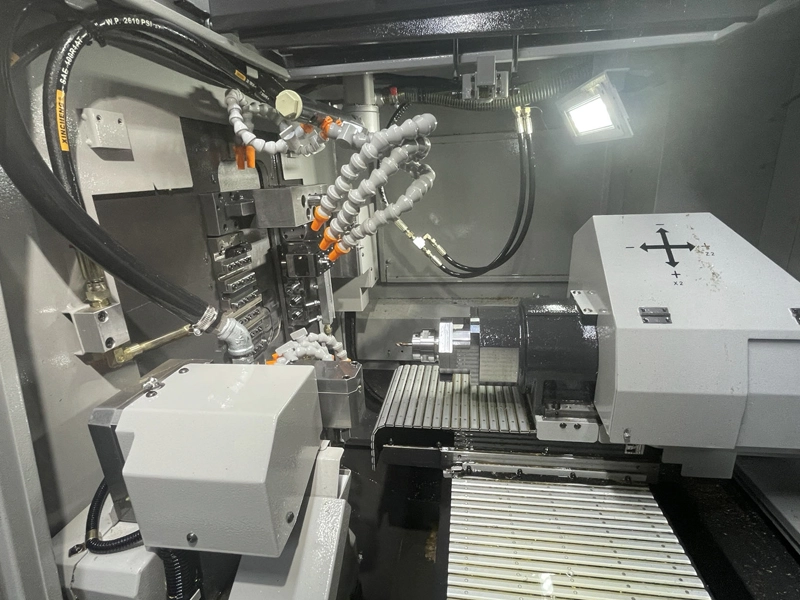
What is CNC Milling and Turning?
Turning and milling compound machining is a machine tool with B-axis linkage and C-axis linkage, which realizes surface milling, drilling and tapping, milling groove and other milling processes on the CNC lathe. It has the compound functions of turning, milling and boring, and can realize a clamping and complete processing. An advanced cutting method that makes the workpiece meet the requirements of use in many aspects such as shape accuracy, position accuracy and the integrity of the machined surface.
Metal CNC Milling and Turning
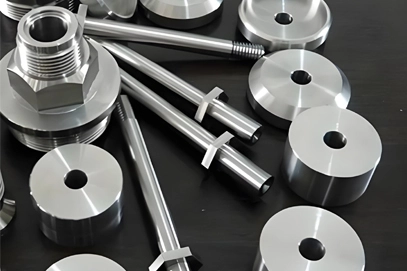
Aluminum
Aluminum is light but strong, with excellent machinability and corrosion resistance. The processed products are beautiful in shape and have a wealth of post-treatment options, which can be sandblasted anodizing, painting, electroplating and other treatments. Due to its excellent material properties, it is widely used in aerospace, automotive, consumer products, automation equipment industries Common alloy:Aluminium 1100、Aluminum 3103,Aluminum 2024,Aluminum 5052,Aluminum 5083,Aluminum 6061, 6061-T6,Aluminum 6063, 6063-T6,Aluminum 6082,Aluminum 7075, 7075-T6,Aluminum ADC12 (A380)
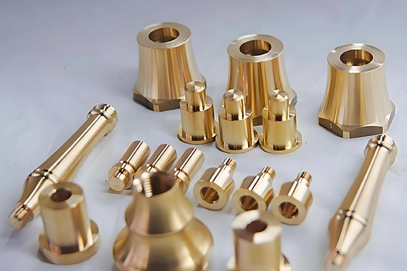
Brass
Brass material has excellent corrosion resistance, excellent machining performance, good stability and electrical conductivity, so its use is very wide, can make faucets, water pipes and other bathroom hardware; It can make Musical Instruments, precision measuring tools, optical instruments, in addition, brass has a wide range of applications in construction, mechanical manufacturing, electronics, automotive fields. Common alloy:CuZn5, CuZn10, CuZn20, CuZn35, CuZn35Pb1, CuZn36Pb3, CuZn39Pb1
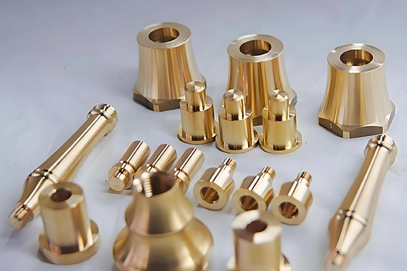
Copper
Copper, also known as red copper, has good electrical and thermal conductivity, excellent plasticity, and is easy to hot press and cold pressure processing. Mainly used in the power industry of cables, transformers, switches, plug components and connectors, motor manufacturing such as stator, rotor, shaft head and hollow wire, electronics industry in the high-frequency transmitter tube, as well as integrated circuit industry. Common alloy:Copper C101 (T2),Copper C103 (T1),Copper C103 (TU2),Copper C110 (TU0)
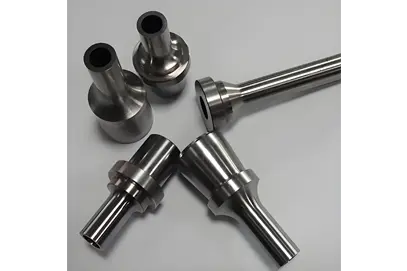
Steel
The characteristics of steel mainly include high strength, light weight, good overall rigidity and deformation capacity, excellent plasticity and toughness, able to withstand dynamic loads well, and poor fire resistance and corrosion resistance. Widely used in construction industry, automotive industry, shipbuilding industry, energy industry, machinery manufacturing industry. According to the different material quality, steel can be divided into: Low carbon steel, medium carbon steel, high carbon steel, low alloy steel, medium alloy steel, high alloy steel.
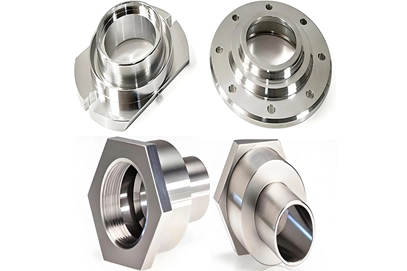
Stainless steel
Stainless steel materials have excellent corrosion resistance, which makes them work continuously in acid and alkali environments. In addition, it has good heat resistance, high strength, environmental protection materials. Therefore, it is widely used in construction, automobile, medical equipment, food processing and other fields. Stainless Steel SUS201,Stainless Steel SUS303,Stainless Steel SUS 304,Stainless Steel SUS316,Stainless Steel SUS316L,Stainless Steel SUS420,Stainless Steel SUS430,Stainless Steel SUS431,Stainless Steel SUS440C,Stainless Steel SUS630/17-4PH,Stainless Steel AISI 304
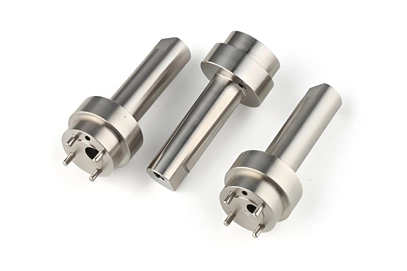
Titanium
Titanium alloy has high strength, good corrosion resistance and high thermal strength, and is widely used in aerospace, chemical industry, Marine engineering, shipbuilding, medical field, energy industry, sports and leisure, automotive industry, drilling industry and other industries and other fields. Alloy grade:TA1, TA2, TA3, TA4, TC1, TC2, TC3, TC4
Plastic CNC Milling and Turning
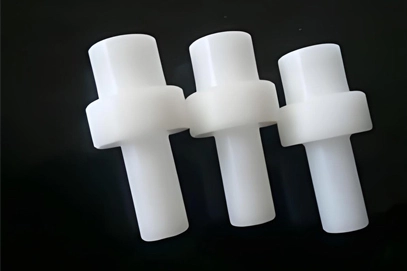
ABS
ABS resin is currently the largest production, the most widely used polymer, the appearance of opaque ivory grain, and has a high gloss. Easy processing, smooth surface, thermal stability, geometric stability, good impact resistance, good insulation, acid and alkali resistance, low creep, high hardness, good rigidity, low price, poor weather resistance, thermal performance is not good enough, general fluidity, small shrinkage, The largest application areas of ABS resin are automobiles, electronic appliances and building materials. The use of the automotive field includes the instrument panel, the exterior panel of the body, the interior decoration board, the steering wheel, the sound insulation board, the door lock, the bumper, the ventilation pipe and many other components. In electrical appliances are widely used in refrigerators, TV sets, washing machines, air conditioners, computers, copiers and other electronic appliances. In terms of building materials, ABS pipes, ABS sanitary ware and ABS decorative plates are widely used in building materials industry. In addition, ABS is also widely used in packaging, furniture, sports and entertainment supplies, machinery and instrumentation industries.
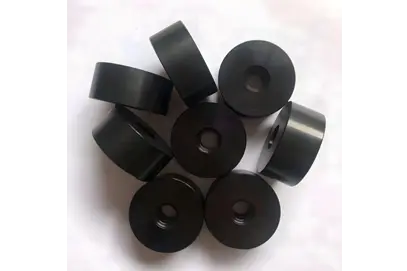
PE
Polyethylene (PE) is the largest variety of general synthetic resins, mainly including low density polyethylene (LDPE), linear low density polyethylene (LLDPE), high density polyethylene (HDPE) and some products with special properties. Good acid, alkali and chemical solvent resistance, good fluidity, good insulation, easy to vacuum the surface, low embrittlement temperature (-75 C°), white translucent, easy to environmental stress cracking, good flexibility. It is widely used in the manufacture of films, packaging materials, containers, pipes, monofilament, wire and cable, daily necessities, etc.
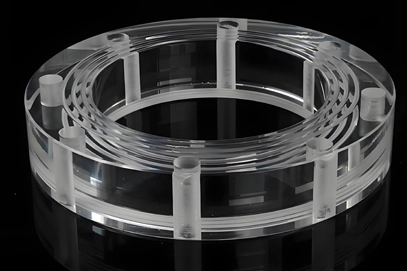
PMMA
High light transmittance, good impact resistance, not easy to break, aging resistance, good weather resistance, low hardness, poor wear resistance, brittle. PMMA products have a very low birefringence, especially suitable for the production of video discs. PMMA has the advantages of light weight, low price and easy molding. Its forming methods include casting, injection molding, mechanical processing, thermoforming and so on. Especially injection molding, can be mass production, simple process, low cost. Therefore, its application is becoming more and more extensive, at present, it is widely used in instrument parts, automotive lights acrylic rods, optical lenses, transparent pipes and so on.
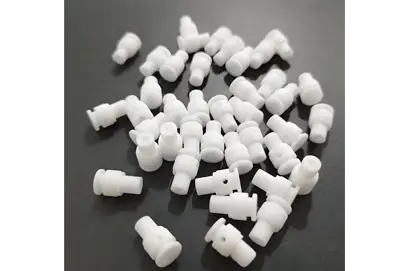
PP
Rigid, bending resistance, good toughness, fatigue resistance, light weight, still has good mechanical properties at high temperature, good acid and alkali resistance and chemical solvents, good fluidity, good insulation, poor weather resistance, 0C° easy to become brittle, stress cracking resistance. Automotive industry (mainly using PP containing metal additives: fenders, ventilation pipes, fans, etc.), equipment (dishwasher door liners, dryer ventilation pipes, washing machine frames and covers, refrigerator door liners, etc.), consumer goods (lawn and garden equipment such as lawn mowers and water sprinklers, etc.)
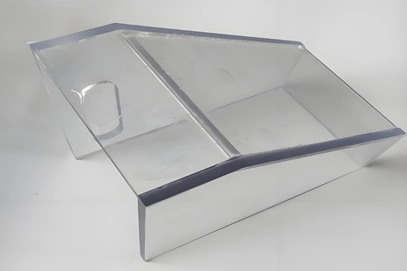
PC
Good impact resistance, good insulation, geometric stability, good heat resistance, low embrittlement temperature (-130 C°), good weather resistance, low creep, high transparency, good mechanical properties, poor solvent resistance, stress cracking phenomenon, poor fatigue resistance, poor fluidity, small shrinkage, easy hydrolysis in boiling water, good gloss, large friction coefficient. The application and development of polycarbonate is to develop in the direction of high composite, high function, specialization and serialization, and has launched a variety of optical discs, automobiles, office equipment, boxes, packaging, medicine, lighting, film and so on.
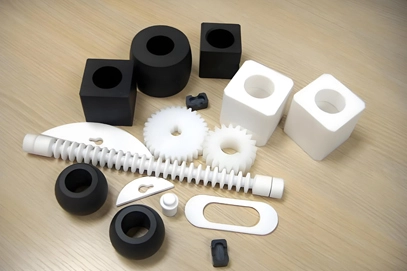
PTFE
Polytetrafluoroethylene [PTFE,] is one of the best corrosion resistance materials in the world today, so it has the reputation of "plastic king". It can be used in any kind of chemical medium for a long time, polytetrafluoroethylene seals, gaskets, gaskets. Polytetrafluoroethylene seals, gaskets, sealing gaskets are made of suspended polymer polytetrafluoroethylene resin molding. Compared with other plastics, polytetrafluoroethylene has excellent chemical corrosion resistance and temperature resistance, and it has been widely used as sealing materials and filling materials.
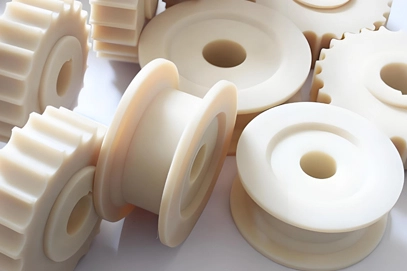
PA (Nylon)
PA has good comprehensive properties, including mechanical properties, heat resistance, wear resistance, chemical resistance and self-lubrication, and low friction coefficient, a certain flame retardant, easy to process, suitable for reinforced modification with glass fiber and other fillers, improve performance and expand the scope of application. This kind of product is widely used, it is a good material for plastic replacement of steel, iron, copper and other metals, and is an important engineering plastic.
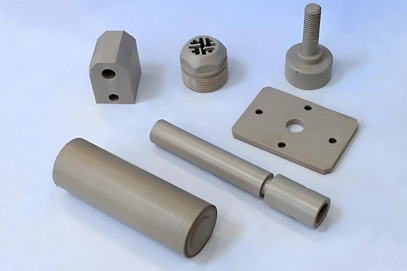
PEEK
Peek material is a kind of high performance engineering plastic, which has the characteristics of high temperature resistance, chemical stability, good mechanical properties and biocompatibility. It can manufacture and process various mechanical parts, such as automobile gear, oil screen, shift starting disk, aircraft engine parts, automatic washing machine runner, medical equipment parts, etc., which are applied in aerospace, automobile manufacturing, electronic and electrical, medical and food processing fields.
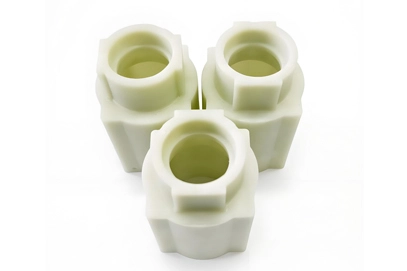
POM
POM material has low strength, but good thermal stability, is not easy to decompose, has a wide processing temperature range (about 50 ° C), and has good stability to acid and base. It is an engineering plastic with excellent comprehensive properties. It has good physical, mechanical and chemical properties, especially excellent friction resistance. Commonly known as steel or steel, it is the third largest general engineering plastic. Suitable for the production of wear resistant parts, transmission parts, and chemical, instrumentation and other parts.
Applications Of CNC Milling
Aerospace: Parts in the aerospace field often require the manufacture of high-precision, complex shaped parts. Turn-milling composite technology can meet these requirements.
Mold manufacturing: mold manufacturing requires high-precision parts, turning and milling composite can complete the automatic processing of parts, improve work efficiency and manufacturing quality.
Complex structural parts processing: some complex structural parts commonly used in the manufacturing process of automobiles, machine tools, etc., turning and milling can complete the processing process of these parts, reduce the processing cycle, and improve the manufacturing quality.
Water conservancy and power field: the field of water conservancy and power needs to process a variety of different structural parts, and the turn-milling composite can be processed according to the needs of the parts to improve the manufacturing efficiency and quality.
Advantages of CNC Milling Service
- Shorten the product manufacturing process chain and improve production efficiency. Turn-milling composite machining can achieve a single load to complete all or most of the processing processes, thus greatly shortening the product manufacturing process chain.
- Mass production of various small parts and complex parts high-speed processing, diversified processing, especially the long and thin complex process can be processed at one time, and automatic feeding devices can be configured to improve efficiency.
- The turn-milling composite can cover the processing of the five-axis machining center, but the five-axis can not do the turn-milling composite processing.
- 510, Building M, Flying Pigeon Industrial Park, No. 1223 Guanguang Road, Guanlan Street, Longhua District, Shenzhen, Guangdong, China
- +8618688772802
- info@precionn.com