CNC Machinig Materials
Precionn offers over 50 types of materials for you to choose from, including metals, non-metals, ceramics, and carbon fiber materials. Our suppliers source raw materials from the largest and highest quality steel and aluminum plants in China, ensuring top-notch material quality.
Precionn not only excels in delivering high-quality custom designs but also provides tailored material and process selection based on the client’s design concepts. Metal options include commonly used aluminum, copper, steel, and specialized titanium alloys. Plastic materials include ABS, PP, PC, PE, PEEK, PA, PMMA, among others. Additionally, we offer special types of materials such as ceramics and carbon fiber. Feel free to inquire for more information on material processing.
Different Machinig Materials

At Precionn, we specialize in meeting your diverse requirements for metal materials and manufacturing processes. Commonly used metals like aluminum alloy, alloy steel, stainless steel, and copper are well-suited for CNC machining. Special steels, such as tungsten steel, are ideal for grinding and wire cutting. Additionally, titanium alloy is suitable for both CNC machining and powder metallurgy. Whatever your needs, we have the expertise to deliver high-quality results.
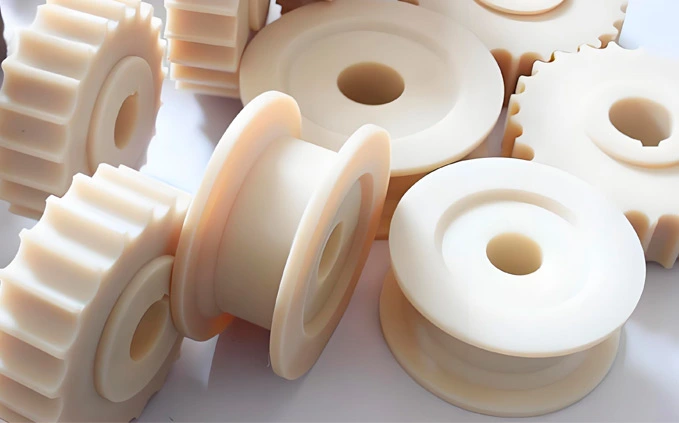
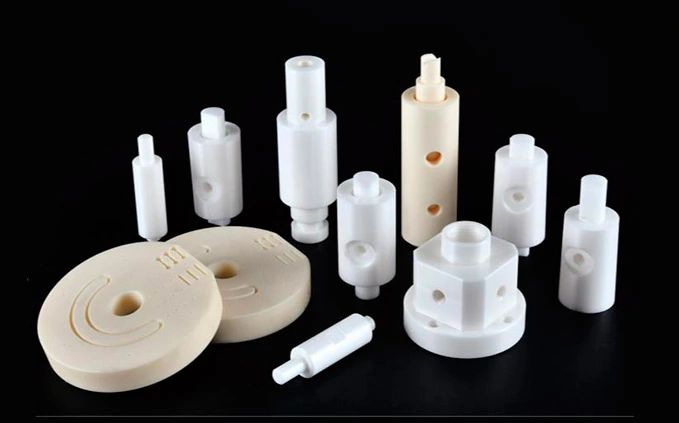
Ceramic materials are sintered inorganic non-metallic substances renowned for their high melting points, exceptional hardness, superior wear resistance, and excellent oxidation resistance. These properties make them highly valuable in industries such as semiconductors, medical equipment, and optical communications. At Precionn, we specialize in producing high-quality ceramic parts. We invite you to contact us for all your ceramic material needs.
Carbon fiber, primarily composed of carbon elements, offers remarkable properties such as high temperature resistance, friction resistance, thermal conductivity, and corrosion resistance. Its lightweight yet high-strength nature makes it ideal for a wide range of applications, including car bodies, bicycle components, high-end consumer electronics casings, and UAV casings and parts. At Precionn, we have extensive experience in carbon fiber processing and manufacturing. Reach out to us to discover how we can fulfill your carbon fiber requirements.
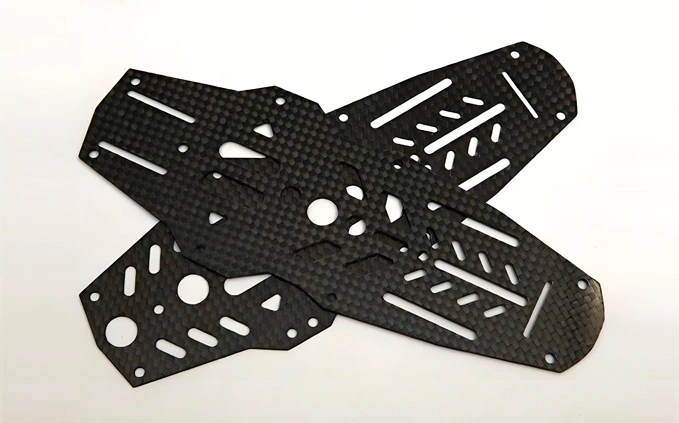
How To Choose The Right Materials for Machining?
To better meet the performance requirements of your product, selecting the right material is crucial. If you have a great idea (product) and detailed design but are unsure how to choose the most suitable CNC machining materials for the parts, we are here to help. This guide will provide some characteristics and machining elements of various materials to help you select the ideal material for your product:
Choosing Based on Machinability:
Low hardness, good plasticity, toughness, and stability. Suitable materials include plastics, aluminum alloys, and brass. Titanium alloys and carbon fiber materials required by some special industries are also suitable for machining.
Choosing Based on Product Application:
If good electrical and thermal conductivity is needed, choose copper. If high strength and light weight are required, for metals, choose titanium alloys; for plastics, choose PEEK or carbon fiber materials. If insulation and high hardness are needed, choose ceramic materials. For wear-resistant metals, choose tungsten steel. For the food and medical industries, choose stainless steel and silicone materials.
Choosing Based on Post-Processing Requirements:
If the product requires high aesthetic standards, diverse colors, and surface treatments like anodizing or painting, prioritize aluminum alloys. If the product needs to be corrosion-resistant and wear-resistant, and requires plating or PVD treatment, prioritize steel. For a natural metal appearance and corrosion resistance, choose stainless steel.
Choosing Based on Processing Techniques:
CNC Machining: A wide range of materials can be chosen, including aluminum alloys, brass, steel, stainless steel, plastics, and titanium alloys. Injection Molding: Mainly plastic materials, including PE, PP, ABS, PA66, POM, PMMA, etc. Casting: Aluminum alloys, stainless steel, and steel. Sheet Metal Processing: Aluminum alloys, steel, and stainless steel. Die Casting: Aluminum alloys, magnesium alloys, and zinc alloys.
Choosing Based on Product Cost:
To meet structural performance requirements, prioritize ordinary carbon structural steel. Only choose high-speed steel or alloy steel if special mold life requirements exist. For aluminum materials, try to choose ordinary aluminum, such as 1-series and 6-series aluminum.
- 510, Building M, Flying Pigeon Industrial Park, No. 1223 Guanguang Road, Guanlan Street, Longhua District, Shenzhen, Guangdong, China
- +8618688772802
- info@precionn.com